You might be wondering if it’s possible to apply powder coating on plastic materials, just like you would with metal. Powder coating has become increasingly popular due to its durability, cost-effectiveness, and environmental benefits compared to traditional liquid painting methods. But when it comes to plastic surfaces, there are unique challenges that need careful consideration before diving into the powder coating process.
In this article, we’ll explore the complexities involved in applying powder coating onto plastics and discuss the potential advantages of doing so. We’ll also take a look at alternative solutions for achieving desirable finishes on plastic substrates.
So, buckle up and prepare yourself for an in-depth understanding of the fascinating world of plastic finishing techniques!
Key Takeaways
- Powder coating on plastic presents challenges, such as lower melting points and adhesion difficulties, but can offer durability, cost-effectiveness, and environmental benefits.
- Material compatibility, surface preparation, and proper curing parameters are crucial for successful powder coating on plastic substrates, and specialized powder coatings formulated for plastics can improve adhesion and performance.
- Powder coating technology allows for unique design opportunities while maintaining high-performance properties, and alternative solutions for plastic finishing include eco-friendly finishes, UV-resistant coatings, custom color matching, and durable lacquers.
- Durability issues must be considered when working with plastic substrates, and proper cure times and temperature settings during the curing process are crucial for a robust finish. Selecting a plastic substrate that can withstand higher temperatures is essential for optimal results.
The Basics of Powder Coating
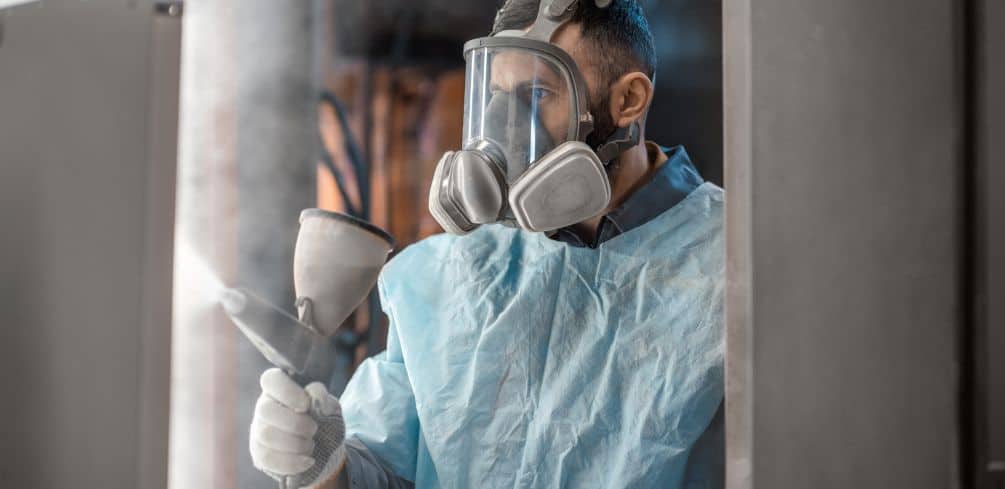
So you’re curious about the basics of powder coating, huh? Let’s dive in and explore this fascinating process together.
Powder coating is a type of dry finishing process that has become increasingly popular due to its durability, environmental benefits, and range of applications. The essential steps involved in powder coating include surface preparation, electrostatic application of the powder material, and curing requirements.
Material compatibility is an important factor when considering whether or not an item can be powder coated.
When it comes to surface preparation for successful powder adhesion, cleanliness is key. Any contaminants such as dirt, grease, or oil on the surface will interfere with the adhesion process and may lead to poor-quality finishes.
This step typically involves chemical cleaning or abrasive blasting to ensure a clean substrate for optimal bonding between the powder coat material and the object being coated.
Once the surface is prepared, electrostatic application takes place where a spray gun applies a positive electric charge to the finely ground powder particles causing them to attach themselves firmly onto the negatively charged object.
The final stage in this intricate process is meeting specific curing requirements. After applying the charged particles onto the object’s surface through electrostatic means, it must undergo heat treatment in order for those particles to flow together and create a seamless layer known as fusion bonding – effectively encapsulating your piece like armor plating!
This thermal cure allows for better resilience against chipping or peeling while maintaining consistent coloration throughout each coated section, resulting in long-lasting protection from corrosion & other environmental hazards alike!
However, keep in mind that not all materials are compatible with the high heat required during curing: plastics often don’t fare well due to their lower melting points compared to metals—so if you’re thinking about applying this technique on plastic items specifically—you might want to look into other alternatives first before diving headfirst into this incredible world of advanced finishing technology!
Challenges in Applying Powder Coating to Plastic
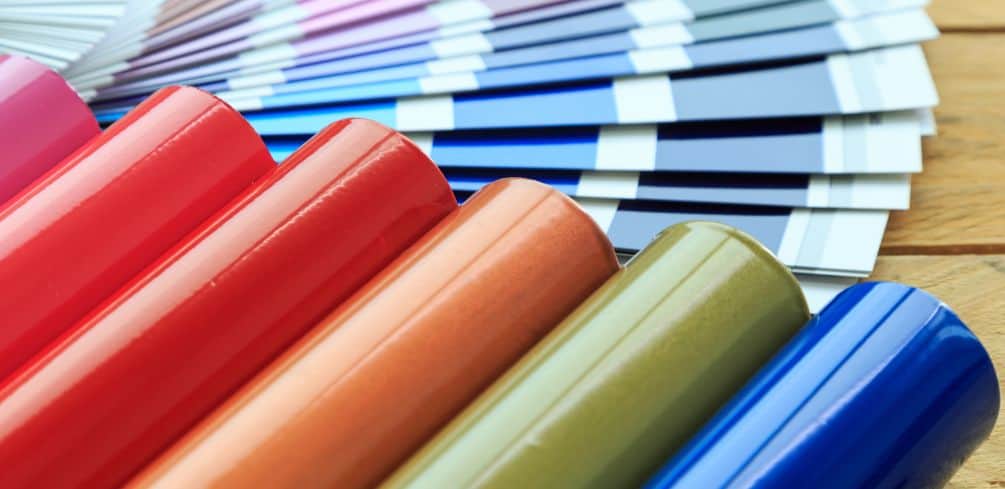
Applying this type of coating to non-metallic surfaces presents several challenges, as it’s typically designed for use on metals. Melting point concerns are a primary issue when attempting to powder coat plastic materials. Most plastics have a lower melting point than metals, which can cause the plastic to warp or melt during the curing process.
Additionally, adhesion difficulties can occur due to the inherent differences in surface properties between plastics and metals. Proper surface preparation is crucial for achieving adequate adhesion and a smooth finish.
One way to address these challenges is by considering material compatibility before proceeding with the powder coating process. Selecting a plastic substrate that can withstand higher temperatures without deforming or melting is essential for optimal results.
Moreover, using specialized powder coatings formulated specifically for use on plastics will improve adhesion and overall performance. These specially formulated coatings often contain additives or other modifications that promote better bonding with plastic surfaces.
Addressing durability issues is also paramount when working with plastic substrates, as they may be more susceptible to wear and tear compared to their metal counterparts. Ensuring proper cure times and temperature settings during the curing process will help achieve a robust finish resistant to impacts, scratches, and environmental factors such as UV radiation or chemical exposure.
By taking these measures into account – careful consideration of material compatibility, surface preparation techniques, and proper curing parameters – you can potentially overcome some of the obstacles faced when attempting to apply powder coating onto plastic substrates while maintaining an engaging appearance and long-lasting performance.
Potential Benefits and Advantages
Imagine the incredible potential of transforming ordinary plastic surfaces into durable, attractive, and environmentally friendly finishes with the power of powder coating technology.
One major benefit is that it offers an eco-friendly option compared to traditional liquid coatings, as it typically contains no volatile organic compounds (VOCs) and has a much higher transfer efficiency rate. This means less waste and lower emissions during the application process. Additionally, since powder coating cures through heat rather than solvents, there’s no need for harmful chemicals that can damage the environment.
Improved durability is another advantage of using powder coating on plastic surfaces. The electrostatically applied powder forms a strong bond with the plastic substrate, creating a resilient and long-lasting finish that resists scratching, chipping, fading, and corrosion better than many conventional coatings.
This increased lifespan ultimately translates to reduced maintenance costs and greater protection for your investment over time.
Aesthetic enhancement also comes into play when considering powder coated plastics; customizable finishes offer endless possibilities in terms of color selection, gloss levels, textures, and even special effects such as metallic or pearlescent appearances.
The versatility of powder coating technology allows for unique design opportunities while maintaining high-performance properties essential for various applications.
By utilizing specialized formulations tailored specifically to adhere well to plastic substrates without compromising their integrity or causing warping during curing processes, it’s possible to achieve stunning results that not only look great but also stand up against daily wear-and-tear far better than traditional alternatives.
Embracing this innovative approach to surface treatment can elevate your products’ aesthetics while contributing positively towards environmental sustainability efforts – all without sacrificing the quality or performance standards you’ve come to expect from more conventional methods. It’s a win-win solution for both your business and the planet.
Alternative Solutions for Plastic Finishing
Brimming with brilliant benefits, alternative solutions for plastic finishing flourish, providing perfect possibilities for both aesthetics and durability. Eco-friendly finishes offer a sustainable option that reduces the environmental impact of your project while still achieving a high-quality result.
UV-resistant coatings ensure long-lasting protection from harmful ultraviolet rays, maintaining the vibrancy and integrity of your product’s colors. Custom color matching ensures seamless integration into any design aesthetic, allowing you to achieve your desired look without sacrificing quality or durability.
Durable lacquers provide an additional layer of protection for your plastic products by creating a hard-wearing surface that can withstand daily use. These finishes are designed to resist scratches, chips, and other forms of wear and tear that might compromise the appearance or functionality of your items over time.
Innovative painting techniques can also be applied to enhance visual appeal while maintaining structural integrity. For instance, hydrographic printing allows for intricate patterns and designs to be transferred onto plastic surfaces without affecting their performance or longevity.
New developments in technology have given rise to cutting-edge alternatives when it comes to plastic finishing solutions. Advances in materials science have led to high-performance polymers with built-in features such as scratch resistance, antimicrobial properties, and self-healing capabilities – all within the framework of a single material rather than relying on additional coatings or treatments.
As knowledge in this realm continues to evolve, so too will the options available for those seeking sophisticated yet practical solutions for their projects’ needs – ultimately delivering results that satisfy both form and function requirements without compromising either one.
Conclusion
In conclusion, you’ve seen that powder-coating plastic presents its challenges. However, with the right materials and techniques, it’s possible to achieve a durable finish on your plastic products.
Keep exploring alternative finishing solutions for plastics to find which one works best for you. With research and attention to detail, you can create a high-quality finish that meets your desired performance standards.